Automotive Assembly Line Shutdowns: The Real Cost Impact
The high stakes of automotive assembly line shutdowns
When an automotive assembly line stop accidentally, the financial impact can be immediate and severe. Major automakers operate on exactly calibrated production schedules where every minute represent significant revenue. Understand these costs help explain why manufacturers invest hence intemperately in preventive maintenance and redundant systems.
The per minute cost of assembly line downtime
The cost of shut down an automotive assembly line vary dramatically depend on the manufacturer, vehicle type, and production facility. Notwithstanding, industry analysts systematically report figures that highlight the extraordinary expense involve:
- For mainstream automotive manufacturers, costs typically range from $22,000 to $$50000 per minute of downtime
- Luxury vehicle production lines can see costs exceed $100,000 per minute
- High volume plants produce popular models may experience losses of up to $1.3 million per hour
These figures represent the direct costs of lose production, but the full financial impact extend practically far. A plant produce vehicles at a rate of one car per minute lose not scarce the immediate production value but likewise face numerous cascading expenses.
Break down the financial impact
Direct production losses
The virtually obvious cost come from lose production capacity. Modern automotive assembly lines typically produce a vehicle every 45 90 seconds. Each minute of downtime mean one or more vehicles won’t be will complete will accord to schedule. For a plant produce 60 vehicles per hour with an average profit of $2,000 per vehicle, that’s $$120000 in lose profit opportunity hourly.
Labor costs during downtime
When assembly lines stop, workers remain on the clock. A typical automotive assembly plant employ hundreds or thousands of workers earn an average of $25 40 per hour include benefits. For a plant with 1,000 workers, that’s roughly $$30000 per hour in labor costs during nonon-productiveime.
Supply chain disruptions
Modern automotive manufacturing rely on precisely in time delivery systems. When an assembly line shut down:
- Incoming component deliveries may need reschedule
- Storage costs increase for components that can’t be use instantly
- Suppliers may charge penalties for delivery changes
- Transportation logistics require costly reorganization
These supply chain disruptions can add $10,000 50,000 per hour to the total shutdown cost, depend on the complexity of the vehicle and its supply network.
Restart costs
Restart an assembly line isn’t equally simple as flip a switch. The process involve:
- Quality control inspections
- System recalibrations
- Potential scrapping of work in progress
- Gradual ramp up to full production speed
These restart procedures typically add $5,000 25,000 to the total shutdown cost, ffiftyfor brief interruptions.
Plan vs. Unplanned shutdowns
The financial impact vary importantly between planned and unplanned shutdowns:
Planned shutdown costs
Manufacturers regularly schedule maintenance periods to prevent more costly emergency repairs. These plan shutdowns:
- Allow for efficient resource allocation
- Enable coordinate supply chain adjustments
- Permit worker reassignment to training or other productive tasks
- Reduce restart complications through methodical procedures
While stock still expensive, plan shutdowns typically cost 30 50 % less than unexpected ones because they eliminate many cascading expenses.
Unplanned shutdown costs
When assembly lines stop accidentally due to equipment failures, supply chain issues, or other emergencies, cost skyrocket due to:
- Emergency repair premiums
- Overtime labor charges
- Expedite parts delivery fees
- Higher scrap rates for work in progress
- More complex restart procedures
The total cost of an unplanned shutdown can easily reach 150 200 % of the baseline shutdown expense.
Real world examples of assembly line shutdown costs
Major automaker case studies
Several automotive manufacturers have publically disclosed the financial impact of production interruptions:
- Ford report that a fire at a supplier facility cause production stoppages cost some $1 billion in lose profits
- General Motors estimate that a labor strike affect multiple assembly plants cost approximately $50 100 million per day in nNorth Americaexclusively
- Toyota calculates that supply chain disruptions from natural disasters result in production losses value at roughly$11.2 billion
These figures demonstrate the extraordinary scale of financial impact when multiple assembly lines experience extend shutdowns.
The ripple effect throughout production networks
Modern vehicles share platforms, components, and production facilities across multiple models. When one assembly line shut down, the impact oftentimes spread:
- Component shortages affect other production lines use the same parts
- Share resources must be reallocated
- Production schedules across multiple facilities require adjustment
This network effect can multiply the financial impact by 2 3 times the direct cost of the original shutdown.

Source: autoprotoway.com
Factors affecting shutdown costs
Vehicle type and profit margin
The cost vary dramatically base on what’s being produce:
- Economy vehicles with thin profit margins ($$5001,500 per unit ))esult in lower per minute costs
- Luxury vehicles with substantial profit margins ($$5000 25,000 + per unit ))reate practically higher financial exposure
- High volume models represent greater cumulative losses due to quantity, level with modest per unit profits
Production facility characteristics
The specific attributes of the manufacturing facility influence shutdown costs:
- Extremely automate plants have higher fix costs but potentially lower variable costs during shutdowns
- Facilities in regions with stringent labor regulations may face additional costs for worker compensation during downtime
- Plants operate at or near capacity face greater opportunity costs than those with production flexibility
Duration of shutdown
The length of the interruption dramatically affect the total cost:
- Brief stoppages (minutes to hours )mainly impact direct production
- Medium term shutdowns (days to weeks )trigger supply chain complications and potential market availability issues
- Extended shutdowns (weeks to months )can permanently damage market share and brand reputation
Mitigation strategies and investments
Give the extraordinary costs of assembly line shutdowns, manufacturers invest intemperately in prevention:
Predictive maintenance
Advanced monitoring systems detect potential failures before they occur:
- Vibration analysis identify develop mechanical problems
- Thermal imaging reveal overheat components
- Oil analysis detect metal particles indicate wear
- Ai power systems predict maintenance needs base on operate patterns
These systems typically cost $1 5 million to implement but can prevent shutdowns cost tens of millions.
Redundant systems
Critical production components oftentimes feature backup systems:
- Multiple power supplies with automatic switchover capabilities
- Duplicate control systems that can take over instantaneously
- Parallel production paths for critical vehicle components
While expensive to install and maintain, these redundancies prevent the well-nigh costly unplanned shutdowns.
Supply chain risk management
Manufacturers progressively invest in supply chain resilience:
- Strategic parts inventories for critical components
- Multiple supplier relationships for key parts
- Geographic diversification of supply sources
- Continuous monitoring of supplier financial and operational health
The cost of these measures is substantial but justify by the potential losses from extended shutdowns.
The bottom line: why manufacturers prioritize uptime
The extraordinary cost of assembly line shutdowns explain why automotive manufacturers prioritize continuous operation above most all other considerations. With expenses range from $22,000 to over $$100000 per minute, fififtyrief interruptions represent significant financial losses.

Source: tawi.com
For perspective, a four-hour unplanned shutdown at a high volume luxury vehicle plant could well cost $24 million or more in direct and indirect expenses. This financial reality drive massive investments in preventive maintenance, redundant systems, and supply chain resilience.
When evaluate the true cost of assembly line shutdowns, manufacturers must consider not fair the immediate production losses but likewise the cascade effects throughout their operations and supply networks. These comprehensive costs explain why automotive production facilities operate with such emphasis on continuous operation and why prevent yet brief interruptions remain a top priority across the industry.
MORE FROM oncecoupon.com
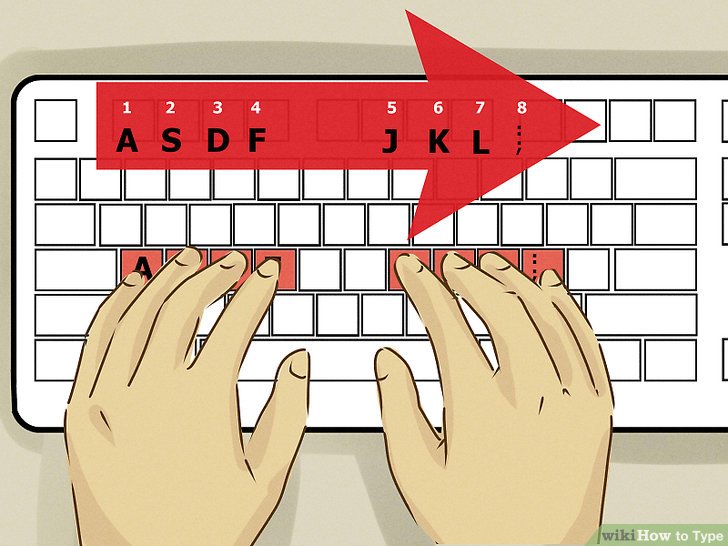
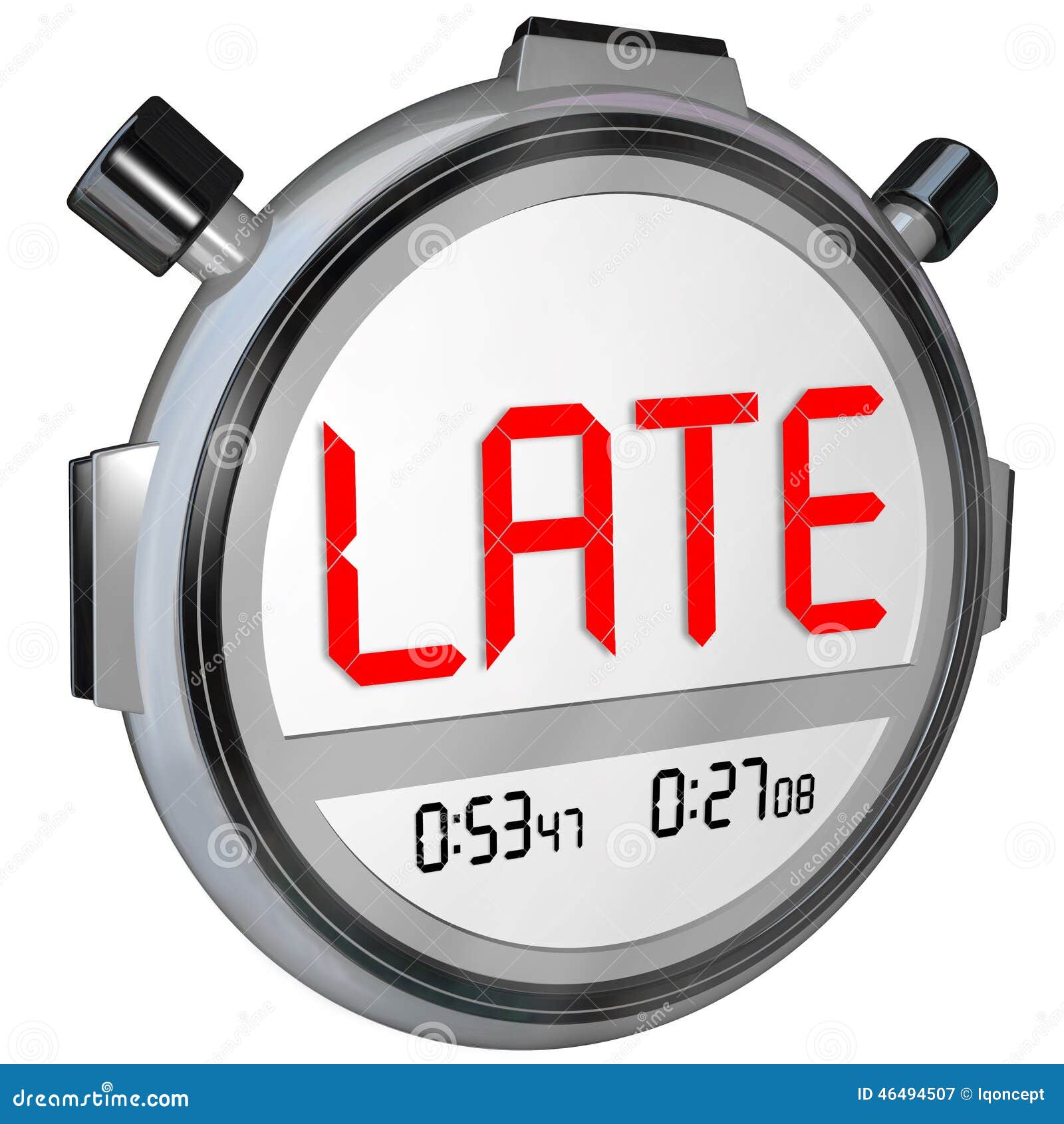
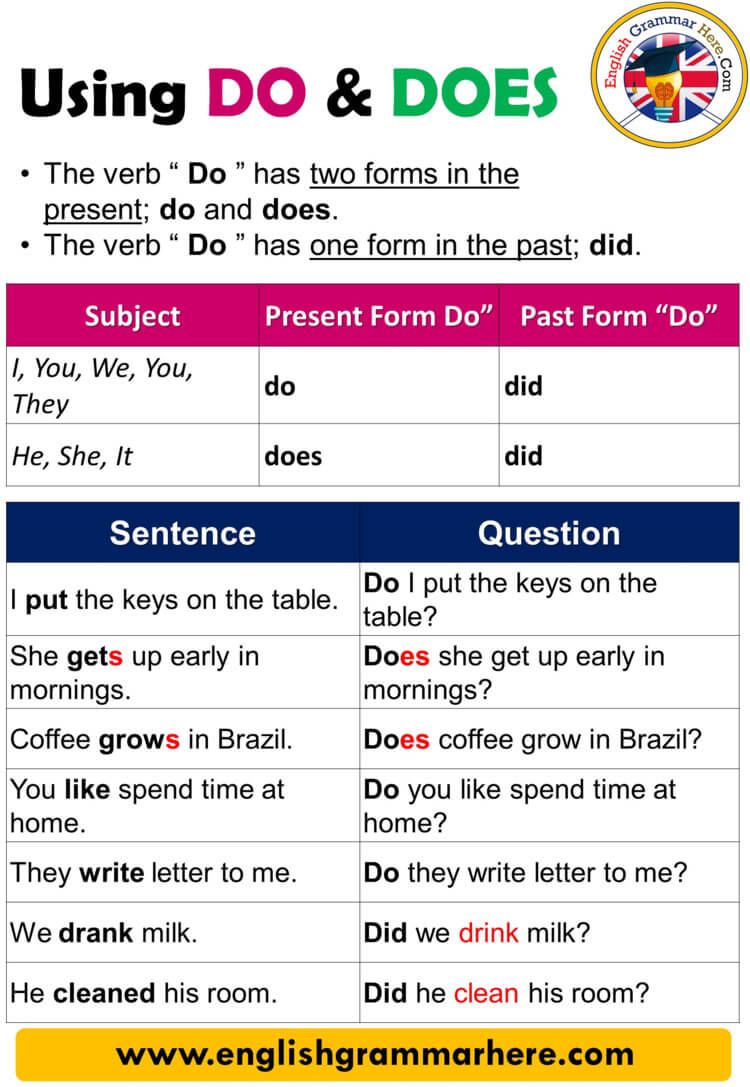
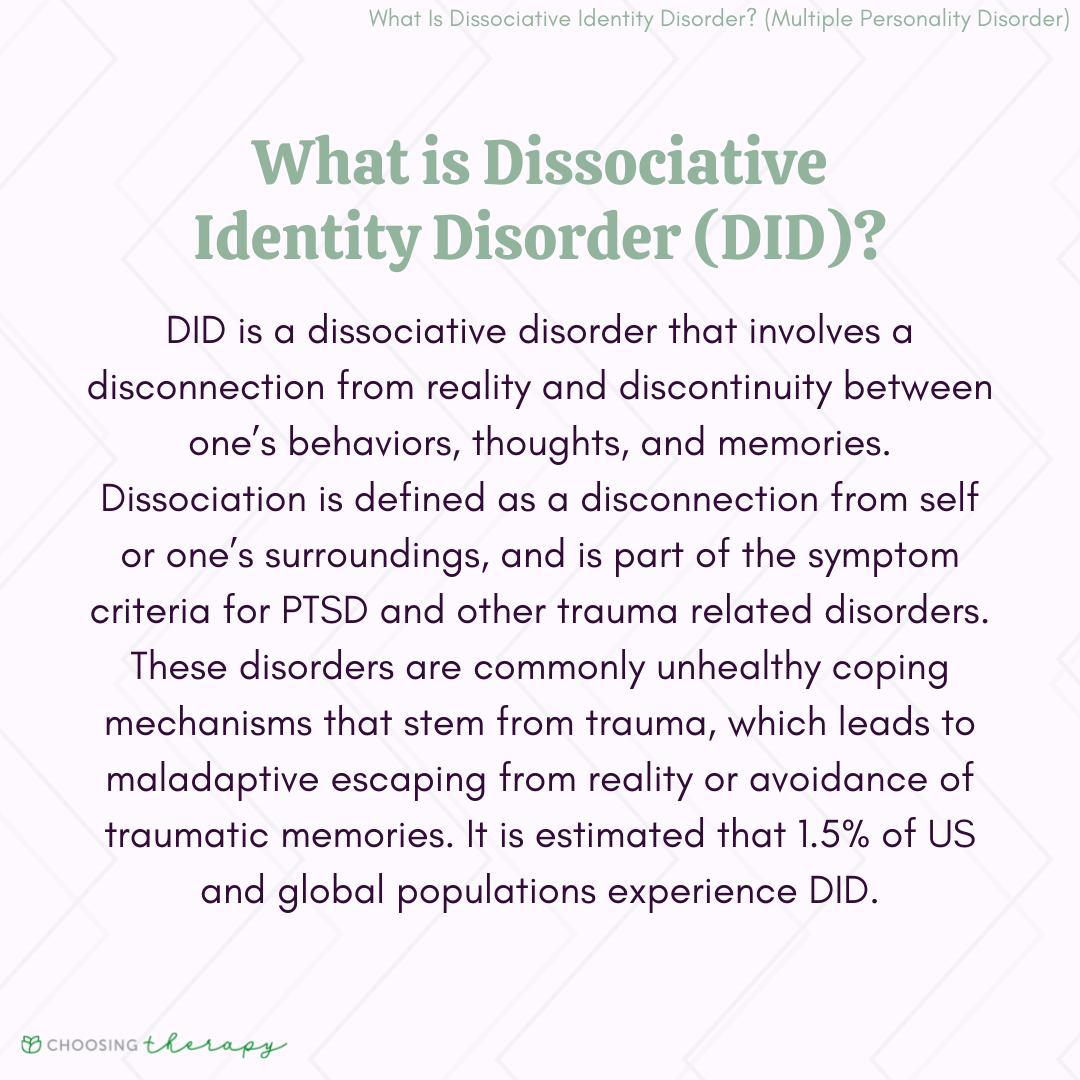
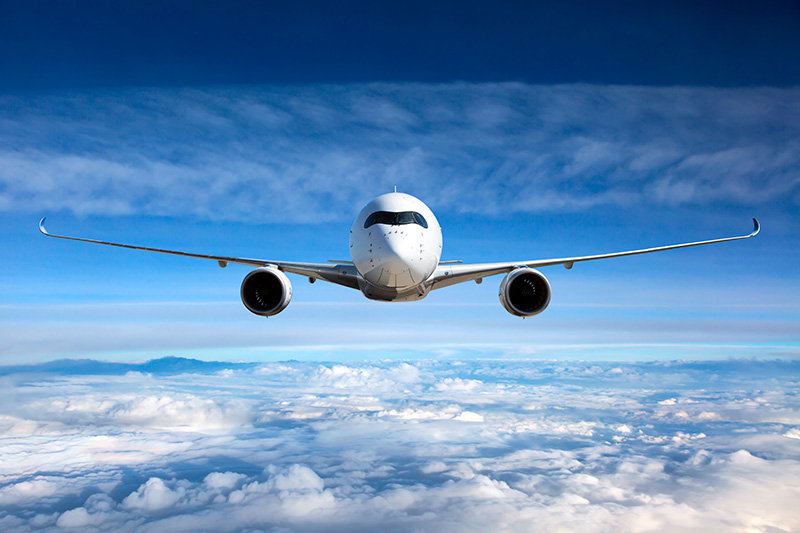
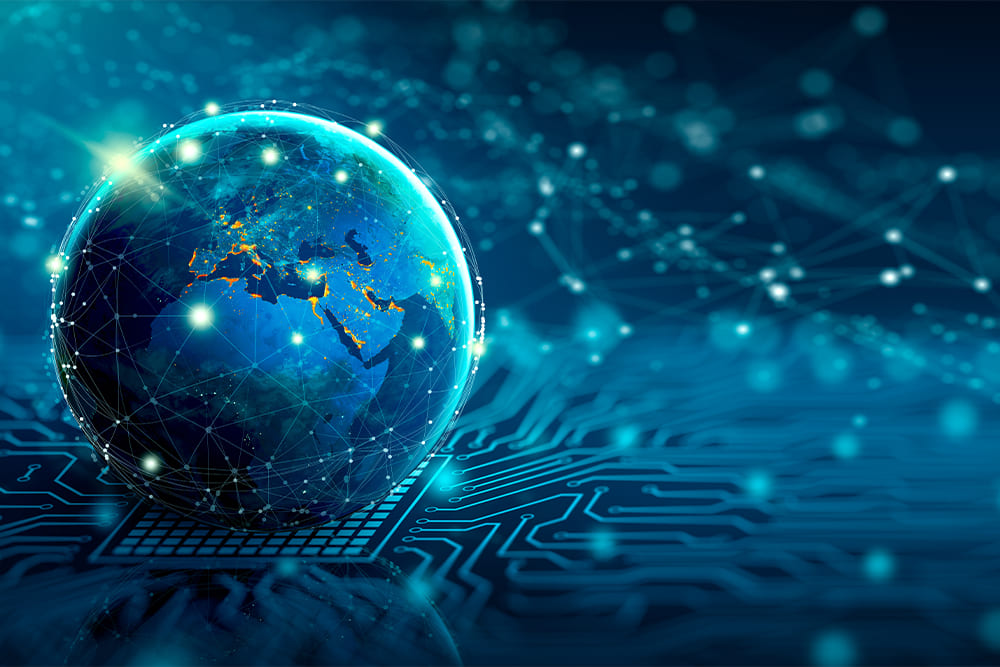
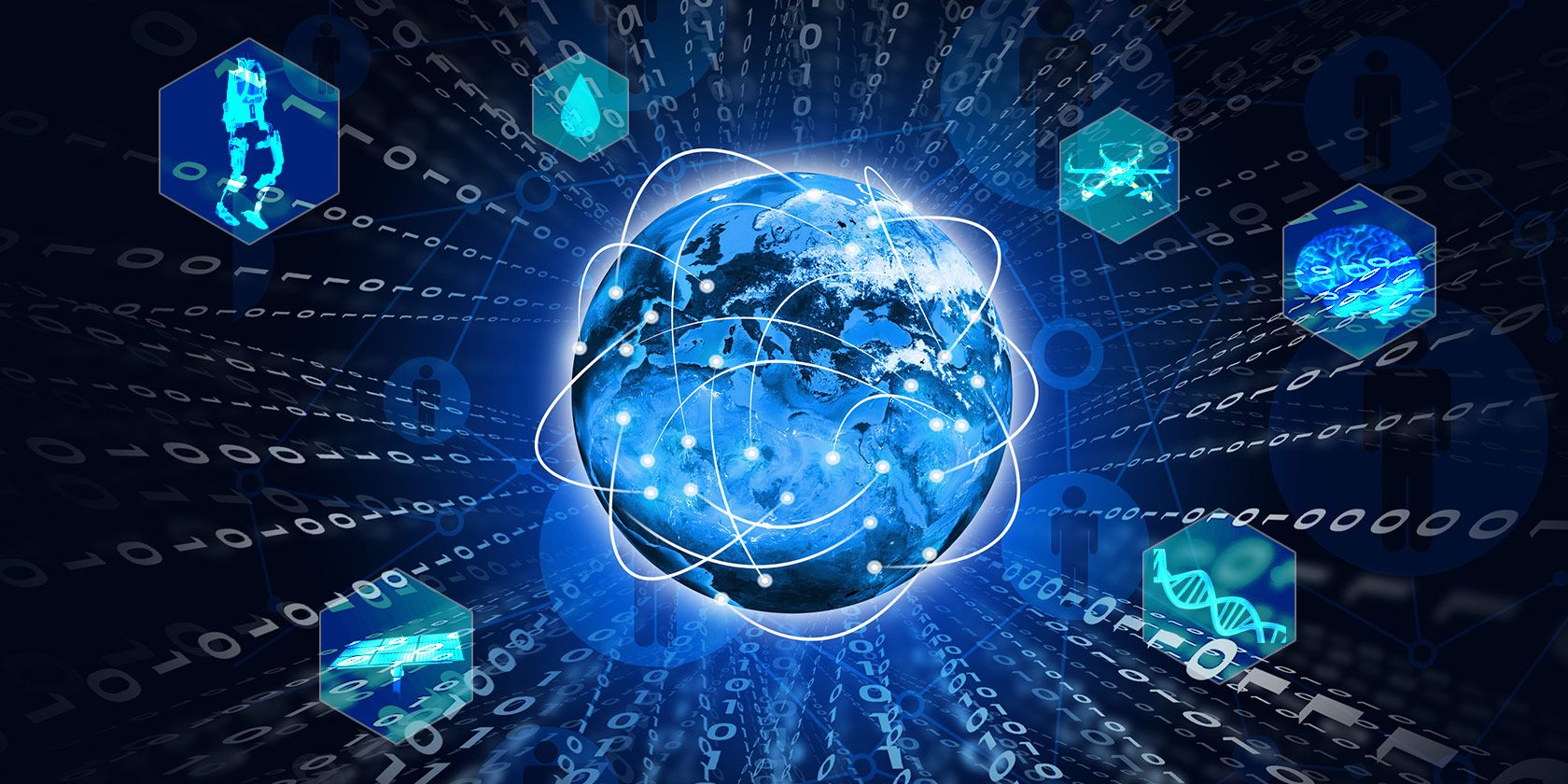
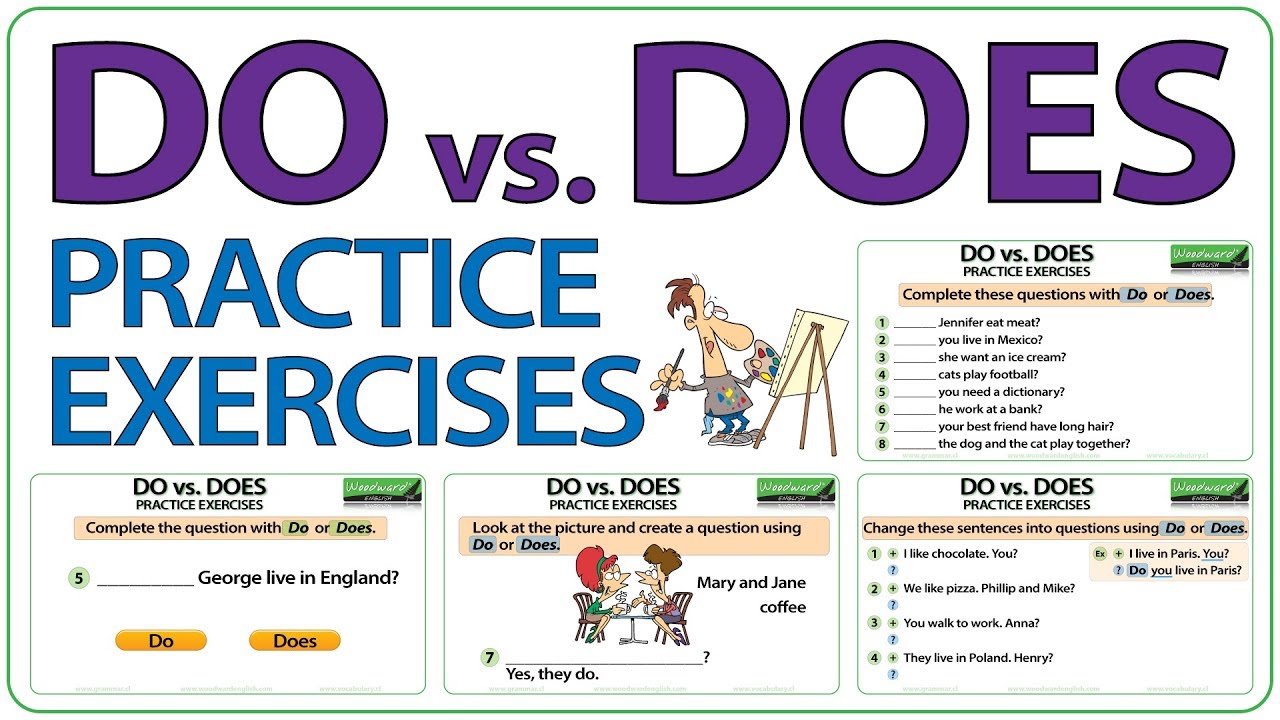
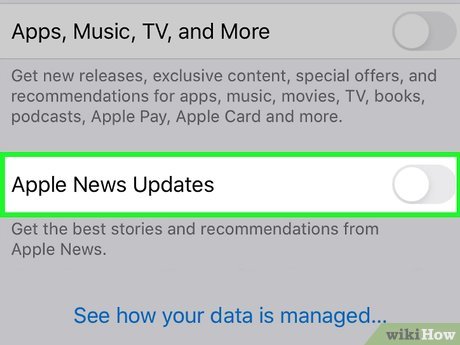
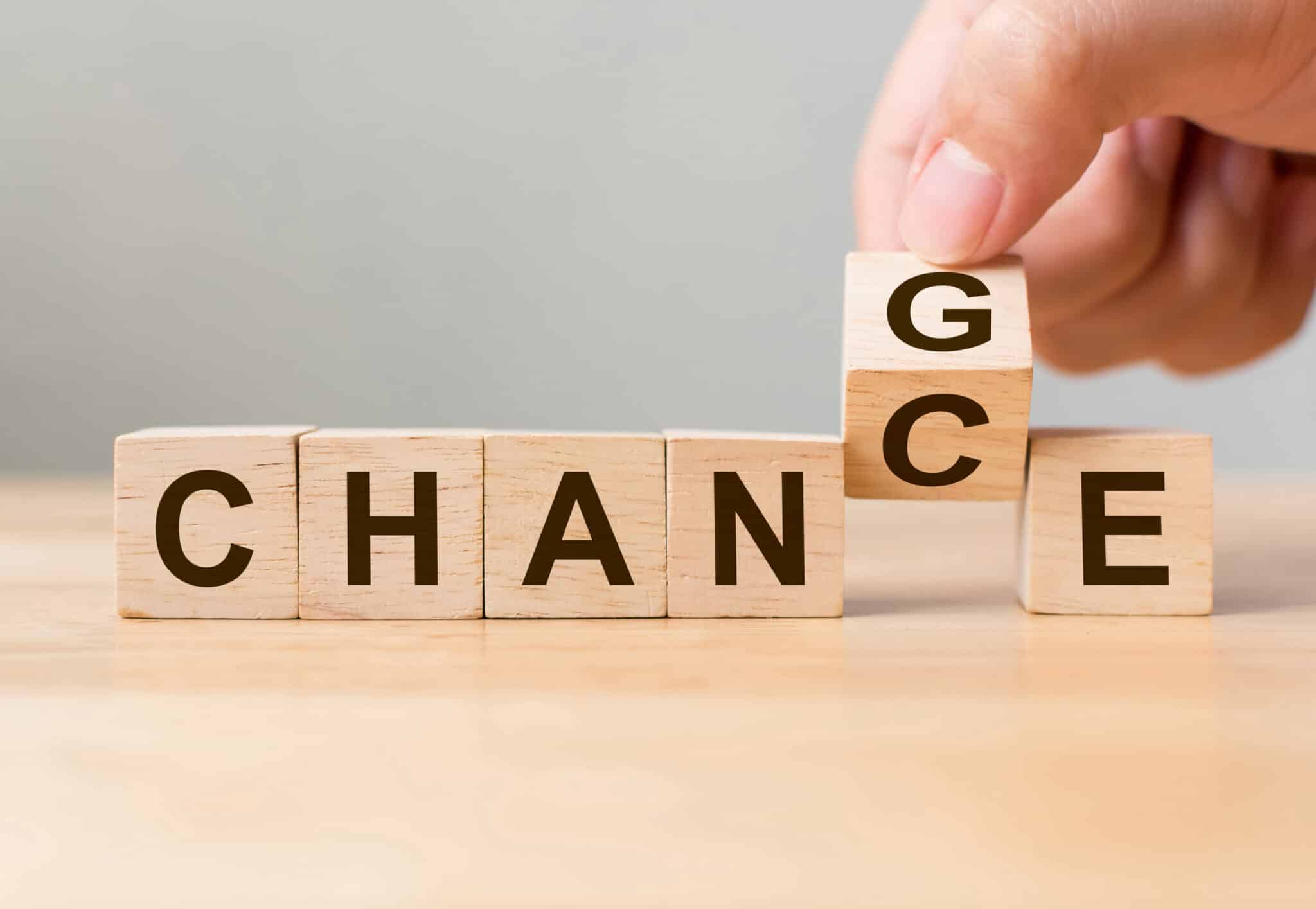
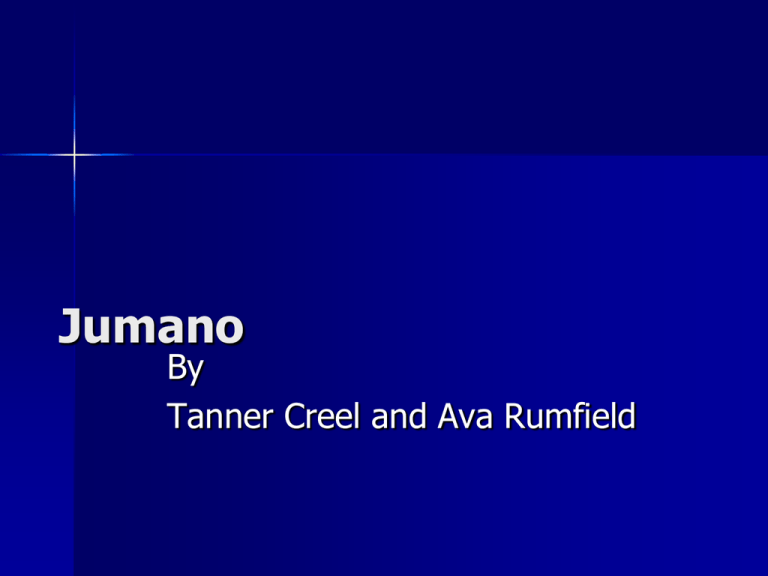
